CX13VDW (AMS 5719)
CX13VDW is your solution for a high-performance, low-cost carburizable stainless steel. Adherent to AMS 5719, this grade meets SAE standards of premium aircraft-quality corrosion-resistant steel. CX13VDW is fully stainless (where not carburized), with high ductility and is easy to carburize. Developed as a superior alternative to Pyrowear® 675 and 9310 steel, it’s used for critical parts such as performance bearings, well drilling parts, engine bearings, and ball screws. CX13VDW offers various advantages over similar metals.
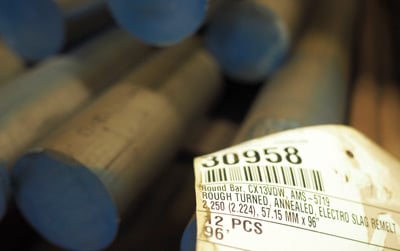
FOR REQUIREMENTS: | Carburizing Stainless Steel, Bearing & Structural |
MELT PRACTICE: | ESR |
SPECIFICATIONS AND DESIGNATIONS: | CX13VDW AMS 5719 AMS 5920 (to be granted) UNS S64152 BS S151 X12CrNiMoV12-3 DIN / WL 1.4933 |
Get CX13VDW (AMS 5719) at Sullivan Steel
We stock ESR bars of CX13VDW with diameters ranging from 0.985" to 5.119" (25mm to 130mm).
Looking for a different size? We can help connect you with what you need! Reach out on our contact page or use the LiveChat to get started.
Benefits of CX13VDW
- Optimized composition and thermomechanical treatment to ensure carburizing process
- Respectable mechanical properties, fully stainless, and a high level of hardenability
- Simple martensitic solution & Classic heat treatment (no Cobalt)
- Capable of achieving a surface hardness of 61-62 HRC
- Easy to carburize – Low pressure or gas pressure with pre-oxidation
- High strength, ductility, and tempering temperature (up to 300 °C / 572 °F)
- Can be gas-quenched for reduced distortions
- Carburized layer has good toughness
- Excellent corrosion resistance in non-carburized areas
How Does CX13VDW Compare to Other Materials?
CX13VDW meets AMS 5719, a cost-effective alternative to AMS 5930 and 9310 steel in some applications. It will also be granted an additional AMS, 5920, due to its unique processing and carburizing qualities relative to standard 5719 materials. See the advantages CX13VDW offers over these familiar grades:
CX13VDW vs. Pyrowear® 675 (AMS 5930)
- Easier heat treatment (three steps vs. five)
- More affordable/cost-effective
- No cobalt, easier workability
- In stock, no minimums
CX13VDW vs. 9310 VAR Steel
- Superior corrosion resistance (9310 is not stainless)
- Over twice the temperature rating
- Higher Strength with similar flexibility
Chemical Composition
C | Si | Mn | Cr | Mo | V | N2 | Ni | |
---|---|---|---|---|---|---|---|---|
min. | 0.10 | – | 0.50 | 11.00 | 1.50 | 0.25 | 0.010 | 2.00 |
max. | 0.15 | 0.30 | 0.90 | 12.50 | 2.00 | 0.40 | 0.050 | 3.00 |
Heat Treatment
Heat treatment for CX13VDW follows these guidelines:
- Carburize at approximately 900–980°C
- To harden, heat to 1050°C, then oil, air or gas quench.
- After carburizing and hardening, CX13VDW can be tempered between 200°C and 300°C.
- For non-carburized CX13VDW, adjust tempering based on properties required for your application.
- The recommended processes can be found within AMS 2759/5 for through hardening and in AMS 2759/7 for carburization.
Mechanical Properties
The following table includes Brinell Hardness in the annealed condition and other mechanical properties following heat treatment, beneath the carburized layer:
Hardness | 255 HB |
Ultimate Tensile Strength | 1350 MPa |
0.2% Yield Strength | 1000 MPs |
Typical Applications
CX13VDW can be a good choice for applications requiring high strength and durability, resistance to corrosion, and precision engineering, including:
- Ball screws (examples: commercial aircraft horizontal stabilizers, electric brake drive screws)
- Shafts and parts for corrosive environments (e.g., seawater)
- Injection bodies for corrosive environments
- Blade propellers
- Gears
- And more!
More CX13VDW Resources
For more details on CX13VDW (AMS 5719), explore the following resources provided by manufacturer Aubert & Duval: